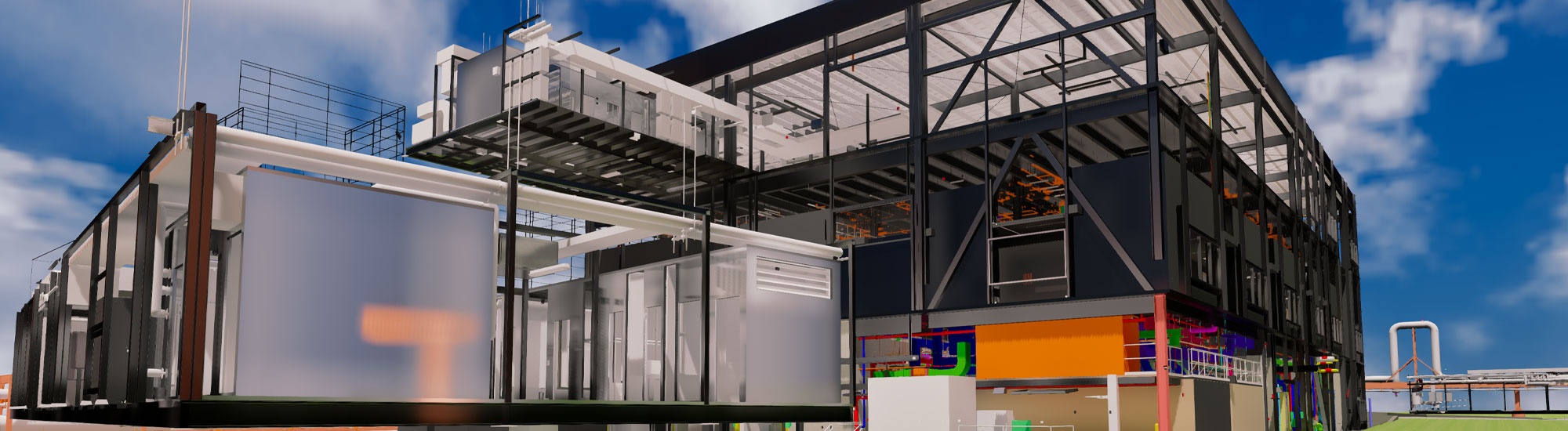
The race for a COVID-19 vaccine has highlighted the importance of accelerating the design and construction process, in order to bring manufacturing facilities online to produce the vaccine as quickly as possible. The silver lining of the COVID pandemic is that it has fostered innovation and collaboration. While companies are racing to find a vaccine and therapies to help patients, the last thing they need is for traditional construction delivery methods to challenge or even sabotage their production goals.
Following are 12 strategies and solutions for accelerating the design and construction process that can yield record breaking delivery times.
1. Map out the process from start to finish. To accelerate a project, remember to look at all aspects of the project and clearly define the critical steps that are required to meet the end date. Often, owners will look to expedite a single phase or equipment procurement and delivery. However, it is important to lay out the sequence for the entire project and the required steps to meet the schedule objectives. For each activity, the necessary labor, information (design), equipment, and materials should be defined. Any steps that are redundant and resources that do not add value should be removed to leverage the full supply chain.
2. Coordinate BIM model level of detail. Under a traditional design approach, the design drawings, and Building Information Modeling (BIM) model are developed to represent 100% of the design intent. This is typically done at a Level of Detail (LOD) of 300 - 350. The next step is to have the trades develop shop fabrication drawings at a LOD 400, using the design model as the design intent, though this adds an additional step and time to the schedule. Consider coordinating the LOD that the A/E’s will deliver with the trades early in the project to eliminate the redundant modeling time and reduce duplication of effort and as a result reduce time.
3. Focus on project drivers. It helps to focus on the driving factors for the project. Is it speed or is it cost? In an example like the Covid-19 vaccine production, the mantra is “everyday matters,” because the virus never sleeps. In these high-profile projects, teams break paradigms and find ways to accelerate the schedule because every day counts. If everyone is aligned to make project decisions based on speed, it allows the team to remove or relax some of the stage gates that support an accelerated schedule.
For example, there may be pushback from procurement due to the need to obtain three independent bids for architectural services. In the interest of expediting the project, the client may decide to waive the competitive bid requirement and award the project to an architecture/engineering firm already familiar with the building. For high profile projects that receive government funding, such as vaccine manufacturing facilities, government contracting guidelines will need to be followed and the appropriate sole source justifications will be needed for future potential audit.
4. Don’t feel you need to reinvent the wheel. Sometimes customization is absolutely necessary, but if time is of the essence, discuss off-the-shelf options with vendors and stakeholders to find a solution that saves time. This can be applied during both design and construction.
An example of this is IPS’s iCON delivery platform, which features several pre-engineered solutions and modular components. The outer building structural system uses standard shapes and systems that are pre-engineered, prefabricated and assembled in the field. The internal modular architecture offers laboratory and clean manufacturing modules that are delivered as ready-to-install plug and play pods and are available in several standard sizes. The system offers multiple pre-engineered application solutions for cell and gene therapy, continuous oral solid dosage manufacturing, laboratory modules, support spaces for media and buffer prep, washrooms, vaccine manufacturing and aseptic filling solutions. These modules can be configured to meet specific owner requirements if necessary. Additional time can be saved by having vendors provide their standard skid solutions for process equipment and support in the pods prior to leaving the factory.
This approach can save upwards to six months of design and construction time. There will be times when customization is absolutely necessary — but if time is of the essence, looking at pre-engineered solutions is a project delivery alternative.
5. Think about integrated delivery vs. traditional design-bid-build. Under a typical design-bid-build scenario with an accelerated schedule, architects and engineers designing a project will find the most expeditious solution that meets the owner requirements. They send it out to bid, where the bidders may offer suggestions on how to achieve the same requirements at a reduced cost, or suggest ways to bundle elements to speed construction.
If project decision makers want to achieve faster results, consider refining the process by evaluating the entire delivery process. Rather than bringing the documents to 100% completion, maybe have the MEP and other critical trades provide design assist alternates to their bids, invite key subcontractors to be part of an integrated design process at the very beginning and receive the benefit of their cost saving suggestions earlier in the project.
This approach was used on a recent GMP pilot plant in California for a company that had received an expedited FDA approval for a new cancer drug. The company wanted to bring manufacturing in-house so they could better monitor the clinical trial. Using an integrated delivery method, the project team brought in a cleanroom manufacturer, a mechanical-electrical contractor, and with the stakeholders, the three team members created drawings based on the project’s performance criteria and were able to deliver the project from design to construction in 12 months.
6. Emphasize collaboration. Many projects benefit from inviting the best of the best in terms of mechanical and electrical vendors and EPCM service providers in the early phases of the project to develop out-of-the-box solutions. On a recent COVID vaccine project, the manufacturer wanted to use a proprietary filling technology that would significantly lower the cost of the vaccine. The client worked directly with the equipment vendor to develop a program of requirements and then collaborated with the EPCM to design and build the facility around the equipment.
7. Hack the bid process. Instead of the traditional bid process, consider having trades submit their estimated unit costs and labor up-front, and engage them earlier. As the design is finalized, the team will be able to quantify how many feet of pipe and cable, how many tons of sheet metal, etc. If trades have committed to so much per pound of sheet metal, so much per lineal foot of carbon steel, stainless steel, and copper, this will provide a base line cost for materials.
Ask for a per-crew unit price for a typical install crew. Based on the size of the job, calculate how many crews would be required for the construction duration and multiply the cost per crew by number of crews. Once needs are defined, tables for a competitive bid situation can be developed between three contractors based on their buying power for raw materials and hire the most qualified firm with the best rates. This approach is a good way to achieve both the speed and competitiveness. It can also be used on cold chain and equipment procurement.
8. Consider pre-engineered systems and components. One solution that has helped significantly reduce construction schedules and has achieved industry-wide implementation is the use of pre-engineered structural and MEP systems. Designed using state of the art 3D BIM technology and fabricated off-site in controlled conditions, the components are then loaded onto skids and delivered ready for installation at the construction job site. In addition to minimizing construction durations, incorporating pre-engineering components contributes to increased site safety by reducing the number of contractor personnel who have to work on lifts and at high levels. Here are tips for getting the most out of using pre-engineered components:
- Ensure fabricator is robust: With modular construction, any imperfection in the prototype will be repeated multiple times so exacting quality is key.
- Coordination + laser scanning: Coordination between building the modules and how they are actually installed is critical to getting the first module set perfectly. Today, laser scanning and BIM models really help with that, but it is essential that the firm the modules gets it right.
- Components: Make sure fabricator has access to and adequate expertise and capabilities in all the components, such as specialty piping materials.
- Monitoring logistics/supply chain: In a traditional build, a contractor would buy pipe and keep it as inventory, and they would not be paid until it was installed. In an offsite or near-site fast track modular construction, make sure all the components are in the shop. Having a dedicated logistics resource coordinating the supply chain of vendors is critical.
- Visit production plant: It is important that the owner sees the modules being built. Encourage owners to visit the plants where modules are being produced. Looking at the prototype can save valuable time on field modifications.
9. Think inside-the-box by increasing modularity of labs. Many lab spaces already use a modular approach for their layout. For example, traditional biology/wet chemistry labs are configured in 11’ x 33‘ modules aligned side by side along a service corridor housing support utilities. This dimension works well and provides standard casework and aisle distances.
However, by standardizing lab size and dimensions as well as utility components such as chillers, piping and controls, individual lab modules can be efficiently manufactured off site and installed quickly, saving time and construction costs.
Referred to as agnostic lab modules because they are easily reconfigured to accommodate different types of research, the lab modules are extremely flexible, resulting in reduced downtime during future conversions. By leaving space in overhead racks to add piping, cable trays and additional infrastructure, a well thought out agnostic lab modular plan allows capacity to be added in the future.
One drawback using a modular approach is that the building may have a slightly larger footprint than one designed for a single product. However, the benefits of designing flexible facilities that can be repurposed really extend their life, assuring there is not an asset sitting idle because the patent expired and the demand was overtaken by the generic market.
10. Manage quality control. Quality control is especially important on a fast-track design and construction project. Approach it similarly to a traditional build — identify the quality tests and procedures in advance so the contractors and owners understand what has to be done. Have a mockup/test of the first module and test piping, HVAC, weld and seal locations and audit inspection processes based on the modular builder’s scope of work.
Assign a logistics specialist to monitor whether their supply chain will be adequate to meet the speed at which the module is being built to ensure just in time delivery. Monitor productivity in terms of how many units per week or how many feet of pipe per line being installed on a daily basis and checking productivity. Quality control actually increases with off-site fabrication. The work is being done in a controlled factory environment, where climate is not an issue. All material is available on site, allowing the teams to construct the modules quickly and efficiently.
11. Anticipate and manage cash flow. When constructing a modular project, remember there are two parallel construction activities: the modules are being built off-site, while the building structure is going up. As a result, cash flow is being impacted from an owner’s perspective because what would traditionally be the later stages of the project (MEP systems, for example) are being completed in a modular production environment at the same time foundations are being poured on the site.
Owners are receiving invoices for both, but are only seeing one. Even while compressing the schedule and expediting delivery, you have to accelerate your cash flow and spending curve so that the MEP contractors are building modules that will be ready upon completion of the building construction and final install connection in the field. For organizations that are not accustomed to this type of fast track modular construction, owners can feel a disconnect as invoices come in and all that is visible is a foundation on the construction site.
12. Learn from other industries. Look to other industries for solutions and then apply the CGMP regulatory requirements. The food and beverage industry has standardized their buildings and manufacturing systems for years due to the lower margins — and the microelectronics industry has been building fast track facilities to get product to market before it becomes obsolete.
What we are seeing and experiencing today are faster and faster project velocities. When we look back at 2020, not only will we see the devastation that this pandemic has brought, but we will also see significant changes in the design and construction industry that will improve the way capital projects are delivered across multiple industries.