iCON
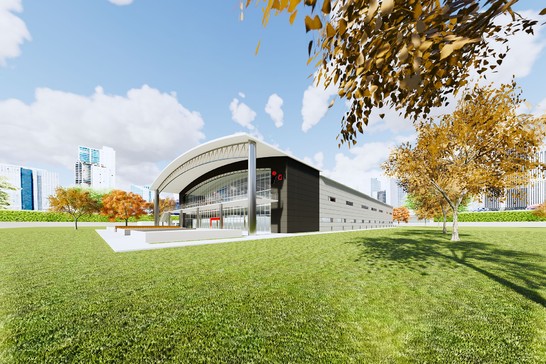
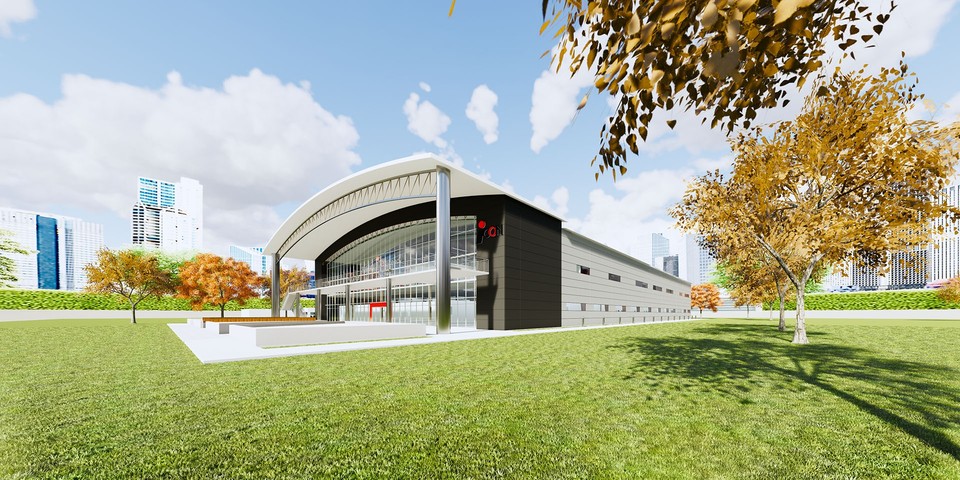
IPS and GCON have partnered to create iCON, a turnkey modular facility platform solution for the biomanufacturing industry. The collaboration provides the most flexible and rapidly deployable facility platform, meeting the modular and mobile demands of the industry. The iCONteam’s broad range of technical capabilities and services along with prefabricated cleanroom PODs provides a true turnkey solution to biopharmaceutical manufacturers and CMOs with needs for production agility and capacity flexing.
The iCON facility platform, the collective efforts of IPS and G-CON Manufacturing, Inc., redefines the turnkey concept that the industry requires. iCON is the most flexible and rapidly deployable facility platform available. iCON meets the production agility demands of the industry due to new production module designs and the use of prefabricated cleanroom PODs®. An iCON facility can be built in less than 12 months which defers capital investments and advances revenue from production. iCON facilities allow for development capacity simultaneous to clinical production and ultimately commercial production for small or large volume products. iCON's modularity allows for movement and redeployment if product demand increases or decreases, in other words, true capacity flexing. In the event that a product reaches the end of its life cycle, the iCON facility can be repurposed for new product candidates or markets. With this capability, iCON's flexibility is unparalleled.
iCON's five choices of operation are unique from any other available facility option. The five choices allow development capacity parallel to producing clinical materials all the way to commercial scale. When the time is right, the development suites are easily converted into additional clinical capacity or small volume to full commercial production. This modular conversion approach avoids additional capital investments up to commercial phase production while allowing efficient development stage transfer without knowledge loss as progress is made. iCON represents a quantum leap in manufacturing flexibility, deployability and repurposability.
Fulfilling Current Industry Demands
- Rapid deployment due to pre-design, pre-fabrication, and pre-qualification
- Capacity flexing due to uninterrupted scaling-up, scaling-down, and scaling-out
- High flexibility of possible 4 x 2,000L process streams for multi-product campaigns
- High quality, with robust designs and materials for long life cycle value
- Reduced total cost ownership due to design, construction and qualification efficiencies
- Repurposable for next generation product life cycles
Expedited Delivery
The iCON team’s high quality, flexible facility can be provided globally and faster than any other solution. We achieve this by simultaneously starting URS alignment, local permitting, shop drawing development, procurement and POD fabrication within weeks of each other. By running these activities in parallel and leveraging our standard designs, we can significantly shorten the schedule to validation start-up.
Cost Basis
Based on the iCON team’s experience, we can provide an order of magnitude estimate at the initial phase of the project for a minimal investment. We do this through our Inceptioneering™ process, where we engage a client for a 2-4 week period to understand their User Requirement Specification and align the iCON offering with the customer’s goals, production requirements and their process platform.
Financial and Operational Benefits
Producing 20 batches per year with an average downstream yield of 66%, our 4x2000L facility is capable of producing 215 kg per year (at 3 g/L). With this amount of production, all major financial performance indicators, e.g., ROI, ROA, and NPV, favor the UBERbioFLEX facility and will be even more compelling as titers increase and batch schedules are optimized. By choosing PODs over the traditional stick built approach, the assets are fully depreciated in 7-8 years versus 35-40 years, a major tax advantage.
Additionally, clients will benefit from a design that is vetted by internationally known experts in the following ways:
- “Optionalization” of a standard design
- Speed to market & delayed capital outlay
- Regionalization of 40% or more of the facility cost (advantageous in varying economic structures)
- High-quality materials of construction
- World-class equipment vendors integrated by world-class EPCMV service providers
- Process flexibility
- Sophisticated business case support through IPS Inceptioneering™ process
Image Gallery
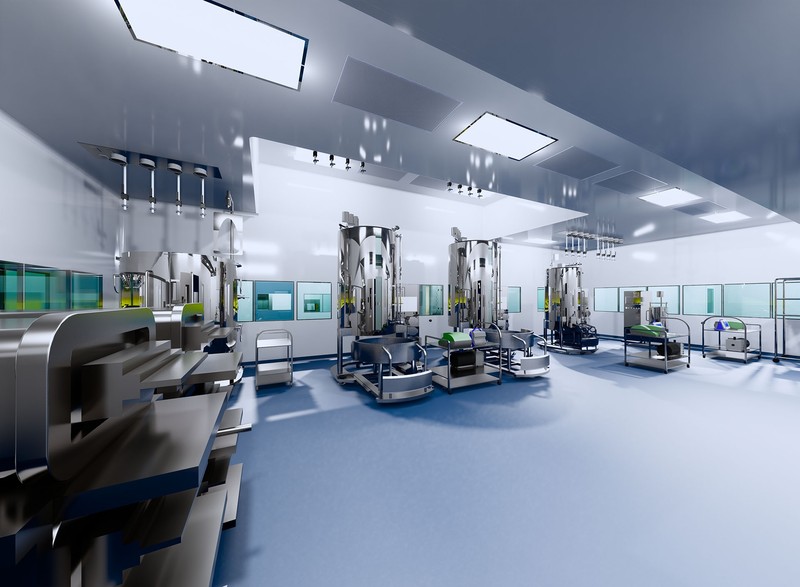
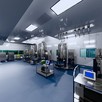
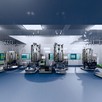
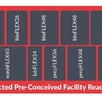
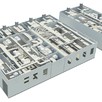
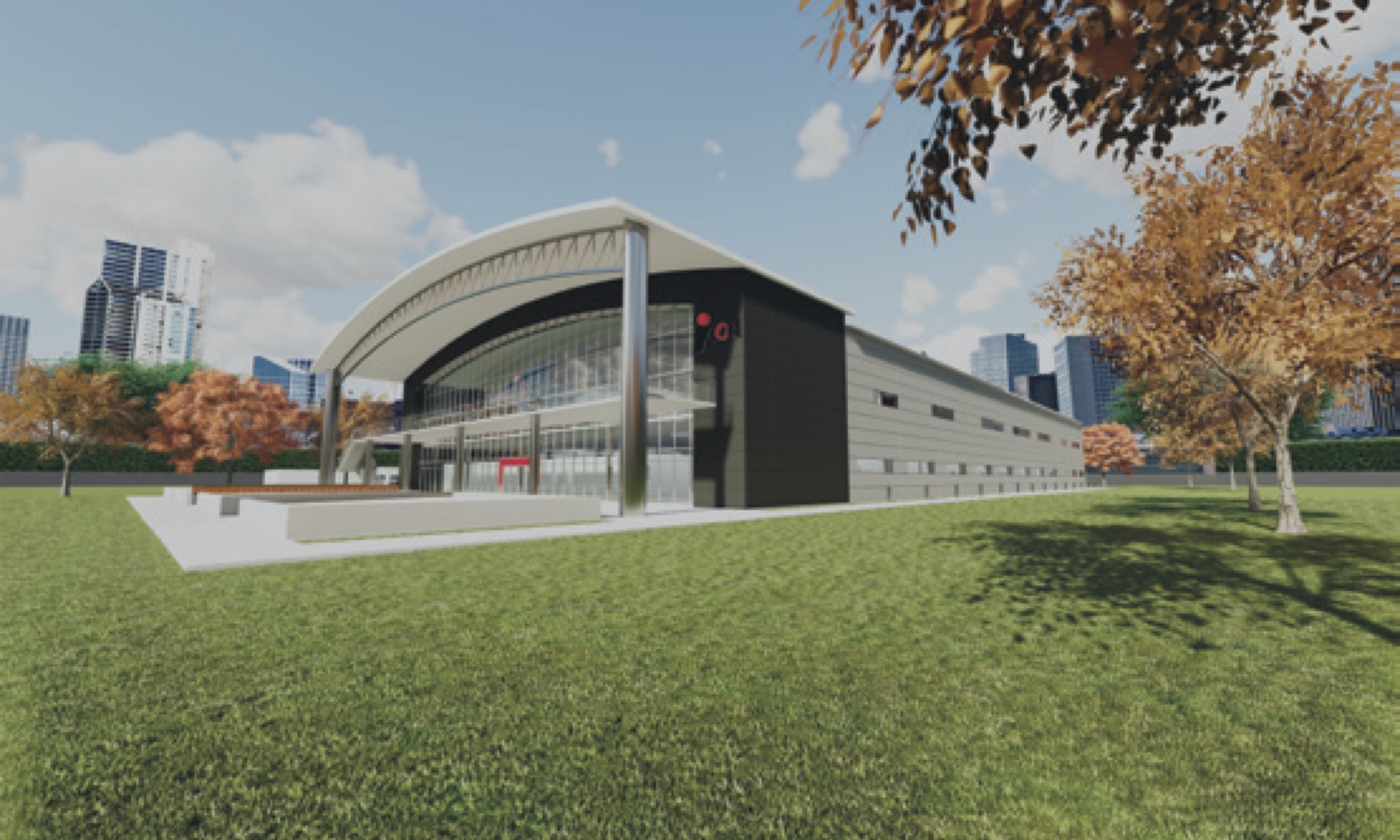
iCON at INTERPHEX
Take a tour through a facility built on the iCON platform with a video that premiered
Featured iCON Experts
Related Happenings At IPS
-
Insights
12 Strategies to Deliver Life-saving Drugs at Lightning Speed
The race for a COVID-19 vaccine has highlighted the importance of accelerating the design and construction process, in order to bring manufacturing facilities online to produce the vaccine as quickly as possible. The silver lining -
Insights
An Innovative Approach to Cell and Gene Therapy Facility Design
Can you keep up with the pace of cell and gene therapy production? Learn how to get product to market quicker and safer than ever before with Tom Piombino’s INTERPHEX Live session, “An Innovative Approach to Cell/Gene Therapy -
Insights
CAR-T Facility Design, Startup, and CQV
Aaron Weinstein kicks off INTERPHEX Live with his session, “CAR-T Facility Design, Startup, and CQV.” There are some interesting challenges in the space planning, utilities, process equipment, and automation of manufacturing f -
Insights
CarTon Announcement at the ISPE Annual Meeting
View the entire CarTon announcement on the Discovery Stage during the 2019 ISPE Annual Meeting & Expo in Las Vegas.