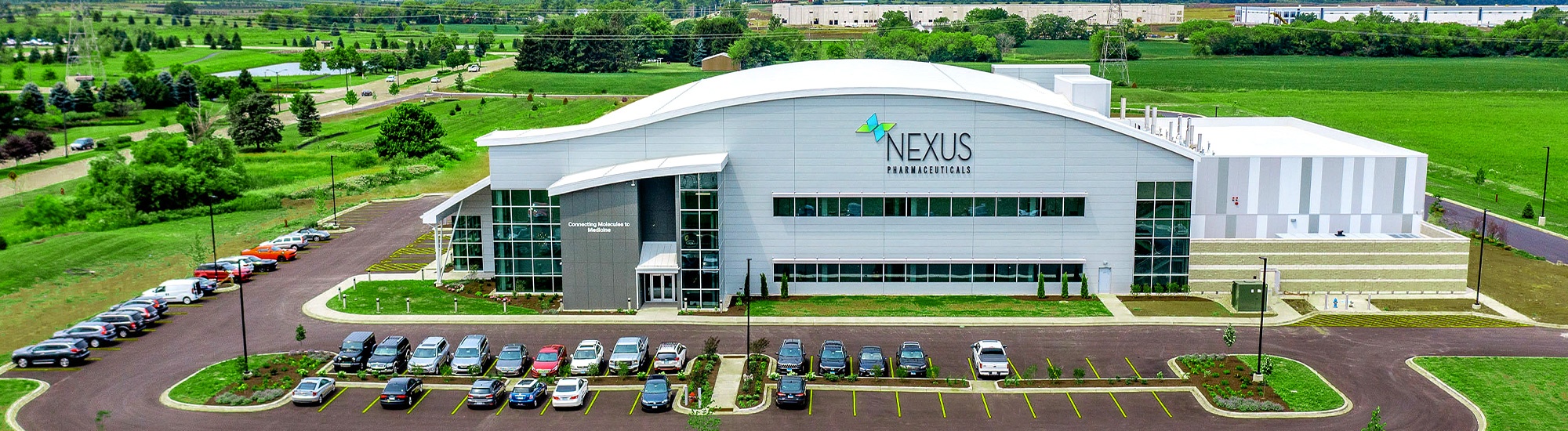
IPS was tasked with designing a three-story, greenfield GMP manufacturing facility in a new major corporate development park. This multi-use facility was a major milestone for supplementing the client’s aseptic fill-finish capacity and features both the application of state-of-the-art process technologies as well as an aesthetically-focused facility concept.
This project allowed the IPS design team to partner with Nexus Pharmaceuticals for their first major manufacturing facility project. This brand-new multi-use facility integrates the variability of a broad and diverse product range, packaging, quality control, logistics and support functions. This facility features a multi-story segregation of GMP personnel and non-GMP support personnel.
This concept was developed between the IPS design team and the Nexus end users so that the facility could meet the requirements of being a stand-alone production plant which featured manufacturing, logistics and administration components.
In addition, the facility had to be easily expandable and was designed with future construction phases in mind so that expansion could occur with minimal impact to the facility once in operation. The current construction features two aseptic filling lines, packaging, sampling and dispensing and clean and dirty utilities. A quality control and microbiology lab were also integrated into the design as well as storage for DEA-regulated products and reagents, refrigerated storage, and limited solvent use.
It’s a unique facility in that it’s a greenfield project with state-of-the-art isolator technology, two filling suites, and the capability to produce aseptic, terminally sterilized and lyophilized products. This prefilled syringe line gives Nexus the capability to produce needled syringes, needleless syringes and cartridges.
Facility Capacity:
- Up to 300 vials filled per minute
- 100% vial IPC with automatic reject
- Advanced isolator system with validated vaporized H2O2 decontamination cycles
- Lyophilization with liquid nitrogen cooling - fully automated loading and unloading
- Capability to produce aseptic, terminally sterilized and lyophilized products
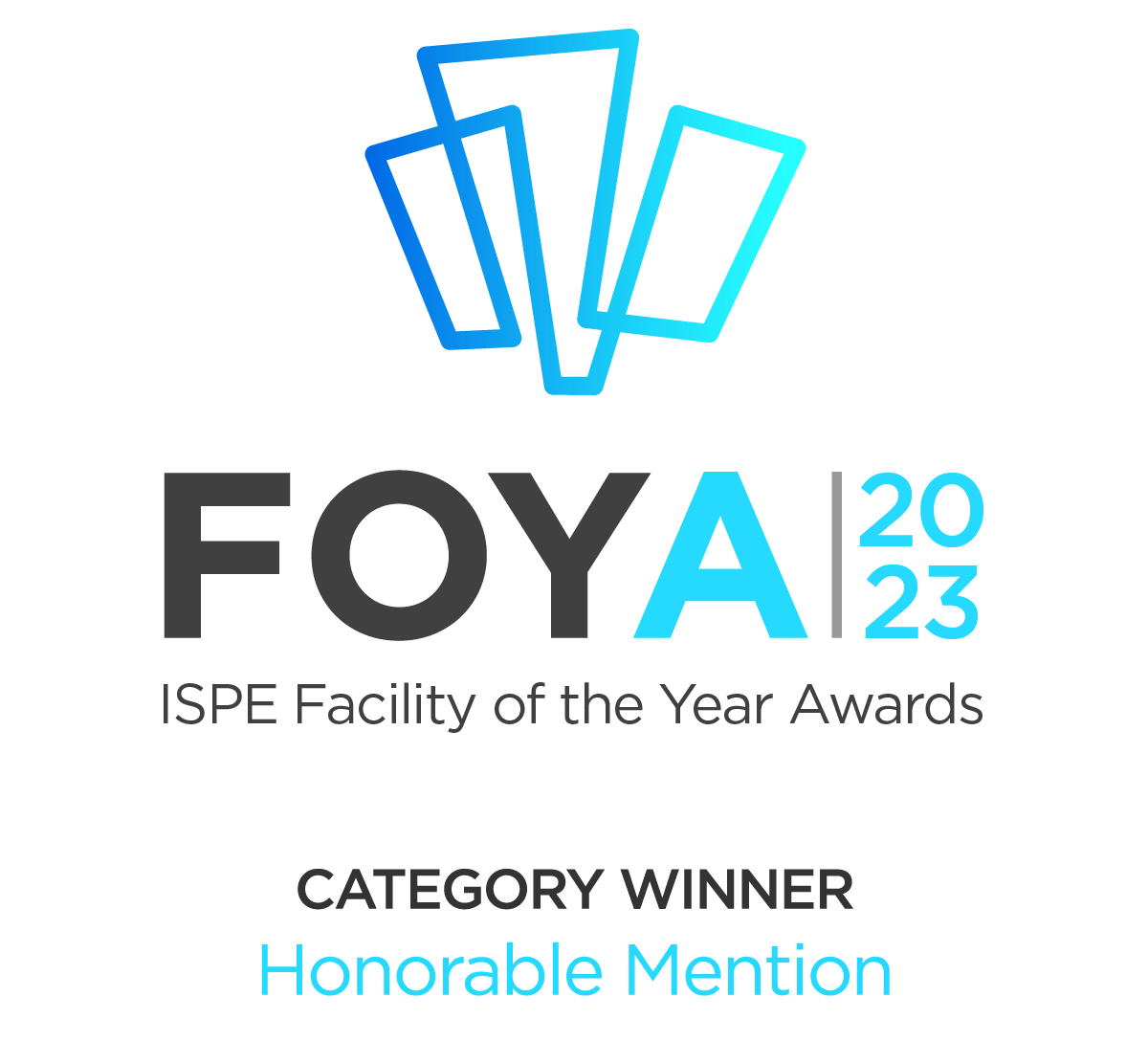
This project was selected as a 2023 ISPE FOYA winner.
Region: AmericasCountry: United StatesOffice: Blue Bell, PA, Leawood, KS
Services: Architecture, Process, Process Architecture, Construction Management, Engineering, Procurement
Phase 1: 85,000sfAwards: 2023 ISPE FOYA, Honorable Mention
Project Details
Region: AmericasCountry: United StatesOffice: Blue Bell, PA, Leawood, KS
Services: Architecture, Process, Process Architecture, Construction Management, Engineering, Procurement
Phase 1: 85,000sfAwards: 2023 ISPE FOYA, Honorable Mention
Image Gallery
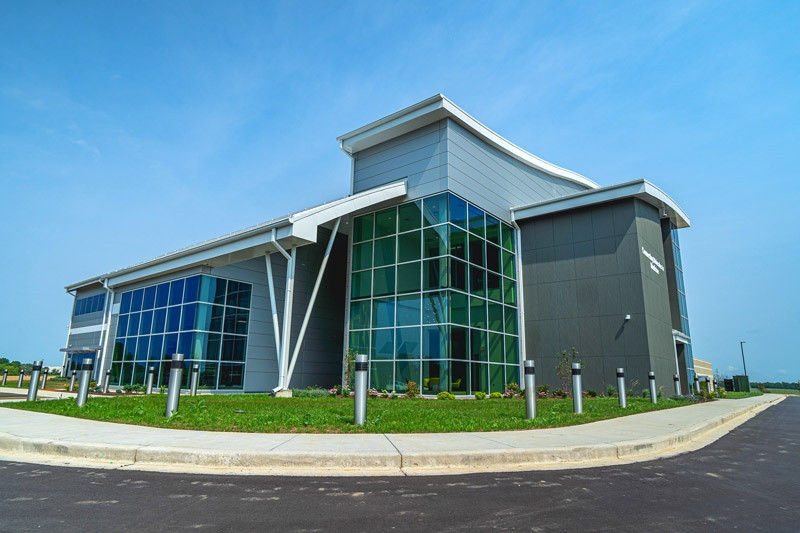
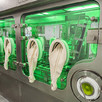
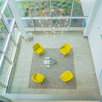
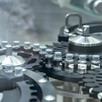
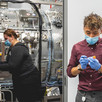
Project Experts
-
Stephen R. Franey, AIA, NCARB
Director, Architecture
-
Raj Gandhi
Manager, Estimating
-
Christopher R. Hall, AIA
Director, Process Architecture
-
Komal Hatti, NCARB, MBA
Director, Process Architect
-
Dan Leorda, PE
Global Strategies and Client Development
-
Mark E. Rezac, PE
Director, Compliance Services
-
Robert Roy, PE
Director, Aseptic Technology
-
Thomas P. Timoney, PE
Mechanical Group Lead
-
Michael Vileikis
Director, Process Technology