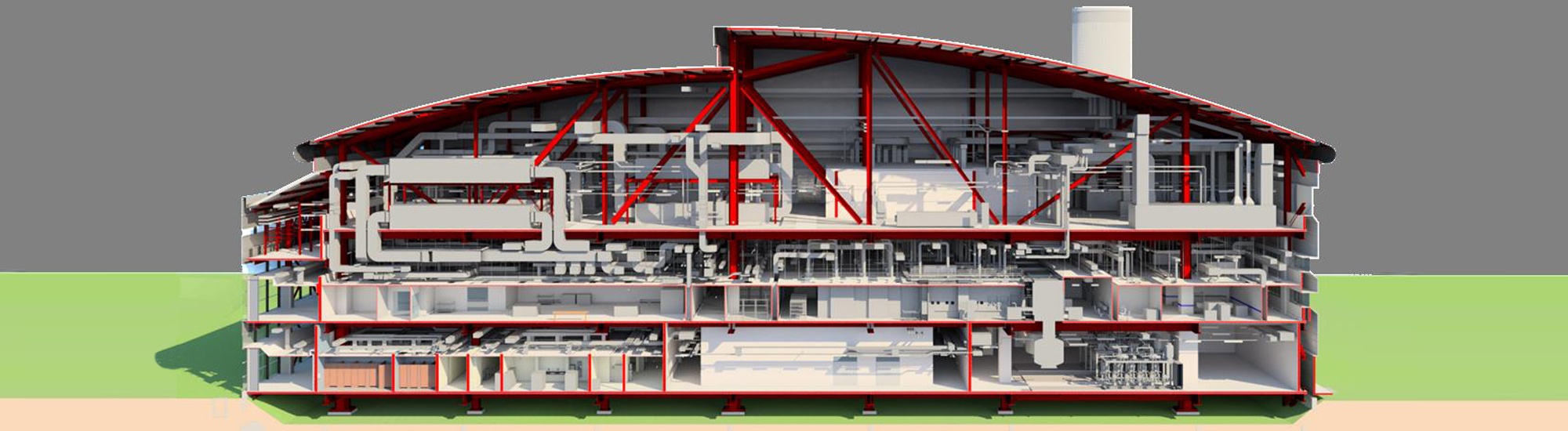
To accommodate higher demand projections and increased volume, a new greenfield aseptic fill/finish site was designed due to projected growth in market demand as well as regulatory pressures on the current facility. In addition, the project instituted advanced aseptic processing in Brazil.
IPS evaluated existing operations and concluded that construction of a new facility for aseptic filling of live attenuated viruses, inactivated viruses, and diluents was needed.
With total production expected to double, IPS was challenged to design a facility that could expand with that growth. The facility needed to handle different sterile and lyophilized volumes between vials, ampoules, and potentially syringes.
IPS designed the facility to incorporate new advances in aseptic technologies, including barrier technology, to limit operator interventions and incorporate recent advancements in equipment automation utilizing continuous processing. The new facility included inspection, secondary packaging, and warehousing on a standalone campus.
- Master planning determined capacity increase, future expansion and necessary modifications to existing operations to meet market demand until the new facility is ready
- Performance URS’ with key information for major process equipment, including vial washer, depyrogenation tunnel, filler, buffer conveyor, lyophilizer, lyo loader, and isolators
- Conceptual layout included alternative layouts and CGMP flow diagrams
- Developed transfer plan and associated logistics to transfer products from existing to the new building
- Performed risk analysis for the transfer of products to include regulatory/inventory risks and personnel/material Issues
- Design based on unidirectional material and personnel flows throughout the facility
Packaging
The packaging building’s shell, component and product staging areas, inspection and packaging lines were designed to efficiently move product along the campus spine.
Filled vials of vaccine are delivered from adjacent buildings on the campus. Vials are scanned, inspected for defects, labeled, cartoned, packed in cases, and palletized. Finished goods pallets are moved to the warehouse building downstream.
IPS packaging engineers designed the lines for current and future functional needs and space requirements while balancing against competing budgetary objectives.
- Largest vaccine manufacturing complex in Brazil
- Advanced automation controls and monitors the flow of product through the building with UV scanning of datamatrix barcodes
- The packaging lines consist of labeler, top-load cartoners, vision inspection systems, and casepackers.
- Incorporates innovative serialization technologies from European and South American suppliers to produce safe, high-quality and globally compliant vaccines
Process Automation
The Process Automation System (PAS) is the site-wide computerized Industrial Automation and Control System (IACS) planned to be used at the facility to provide local direct control of specific non-packaged systems and functions, as well as monitoring and supervisory control of packaged systems.
IPS analyzed the expected system use and defined an all-inclusive strategy to achieve compliance with the agencies’ expectations and industry standards.
IPS developed a PAS Computerized System Compliance strategy document that addressed:
- Regulatory compliance considerations, including US, EU, Brazil, and WHO
- Assessment of the current methodology (procedures)
- Systems and services suppliers management
- System risk assessment and mitigation at various levels
- Validation (CSV) life cycle for COTS, configured and custom system components
- Individual CSV deliverables and activities
- System test and production environment management
- System operational procedures (SOP)
- Quality Assurance for non-regulated system components
Region: AmericasCountry: BrazilOffice: São Paulo
Services: Architecture, Automation, CGMP Audits, Construction Management, Critical Utilities, Commissioning, Commissioning, Qualification & Validation, Design, Energy, Sustainability & Conservation, Engineering, Site Analysis & Master Planning, Strategic & Facility Master Planning, CQV Program DevelopmentIndustries: Aseptic, Biotechnology & Biomanufacturing, VaccinesFacility Types: Manufacturing, Packaging and Warehouse
Size: 1,000,000sf
Project Details
Region: AmericasCountry: BrazilOffice: São Paulo
Services: Architecture, Automation, CGMP Audits, Construction Management, Critical Utilities, Commissioning, Commissioning, Qualification & Validation, Design, Energy, Sustainability & Conservation, Engineering, Site Analysis & Master Planning, Strategic & Facility Master Planning, CQV Program DevelopmentIndustries: Aseptic, Biotechnology & Biomanufacturing, VaccinesFacility Types: Manufacturing, Packaging and Warehouse
Size: 1,000,000sf
Image Gallery

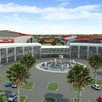
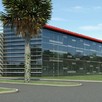
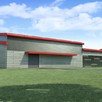
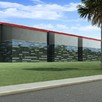
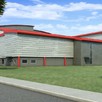
Project Experts
-
Jason S. Collins, AIA
Director of Process Architecture
-
John M. Fay, PE
Sr. Process Engineer
-
Sam Halaby
Sr. Director Global Strategy & Technology
-
Christopher R. Hall, AIA
Director, Process Architecture
-
Gene Martini, PE
Executive Vice President, Design
-
Thomas J. Piombino
Managing Director, Americas
-
Mark E. Rezac, PE
Director, Compliance Services
-
Alicia Riesgo
Associate Vice President, CQV and Compliance Services
-
Joseph J. Rotman
Lead Process Engineer
-
Robert Roy, PE
Director, Aseptic Technology
-
Kevin Swartz
Director of Industrial Engineering
-
Michael Vileikis
Director, Process Technology