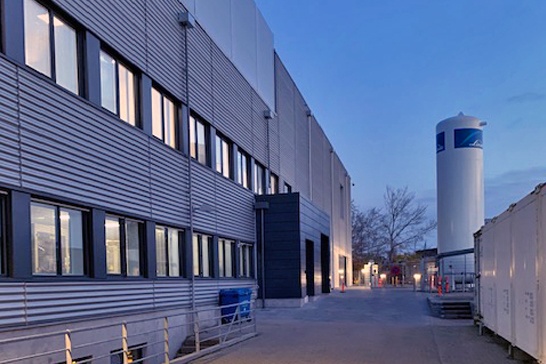
The facility expansion is a multi-product plant designed and built to manage the formulation, filling, lyophilisation, inspection, packaging, and storage of several live attenuated viruses with complex, fragile structures and high value.
The GM02 / BSL2 facility has two functions. It manufactures the clinical and commercial portfolio of Bavarian Nordic’s vaccines, with the capability and flexibility for extremely rapid turnaround between products. It also can operate as a CMO for other similar high-value products. It has the capacity for 40 million doses p/a of liquid frozen products and 8 million doses p/a of freeze-dried products.
The facility consists of: the basement (Level 0) with changing rooms, BDS thawing, and wet utilities; the ground floor (Level 1) with aseptic manufacturing cleanrooms; and an interstitial floor (Level 2) with a walk-on ceiling; and a plant room (Level 3) with air handling units supply and extracting air to the cleanroom and process equipment below.
The requirement for the high-speed filling of complex, fragile molecules with small bulk volumes and minimal product losses drove new approaches to find proven technology clustering to achieve the desired outcomes. The result is a facility that seamlessly integrates "Best Available Technology" to deliver cost-effective and operationally efficient fill and finish capability.
It is world-class in terms of its project execution and efficient use of space within the limited footprint. The uniqueness of this particular project flows around the capital cost, schedule, and spatial constraints. The initial design study completed by another firm incorporated RABS technology for aseptic fill and finish operations. However, the additional facility footprint required for RABS-based facilities (versus barrier isolator-based facilities) proved to not be feasible due to site area restrictions.
IPS came in and redesigned the facility to be isolator-based. The redesign significantly reduced the footprint to fit in the available space, resulting in the reduction of the overall operation and facility cost. The design was so efficient that there was space left over for an additional clinical R&D filling space.
To meet time constraints, equipment vendor designs were expedited, and the engineering, design, procurement, buying, construction, and qualification phases were vertically stacked on top of each other. This type of structure required a robust, strategic, and thoughtful risk-management strategy. To expedite the construction, the piping systems for the basement floor were issued while the rest of the piping design for the other floors were being worked on. The risk paid off with limited rework experienced but maximum schedule benefit. The facility was designed, constructed, and validated within 30 months for the agreed cost and to a level of finish that stands it apart in terms of patient safety.
The diverse project team included people from over all over the world, including the United Kingdom, Denmark, Italy, Germany, India, Ireland, and America. The team worked in a morale-centric, "no fear," collaborative, and shared-risk environment that embraced cultural and technical differences. An emphasis was put on continually enhancing the team’s morale and safety through transparent and frequent communication, “high-touch, low-tech” collaborative spaces such as whiteboards, morale surveys, incentives, and fun team-building work events.
This project was awarded the 2021 ENR Global Best Projects Award in the Manufacturing category.
Regions: EMEA, AmericasCountry: United Kingdom, Germany, Switzerland, United StatesOffice: Basel, Birmingham, Frankfurt, Blue Bell, PA
Services: Consulting, Architecture, Engineering, Process, Procurement, Construction Management, Commissioning, Qualification & ValidationIndustry: VaccinesFacility Type: Manufacturing
Award: 2021 ENR Global Best Projects: Award of Merit
Project Details
Regions: EMEA, AmericasCountry: United Kingdom, Germany, Switzerland, United StatesOffice: Basel, Birmingham, Frankfurt, Blue Bell, PA
Services: Consulting, Architecture, Engineering, Process, Procurement, Construction Management, Commissioning, Qualification & ValidationIndustry: VaccinesFacility Type: Manufacturing
Award: 2021 ENR Global Best Projects: Award of Merit
Image Gallery
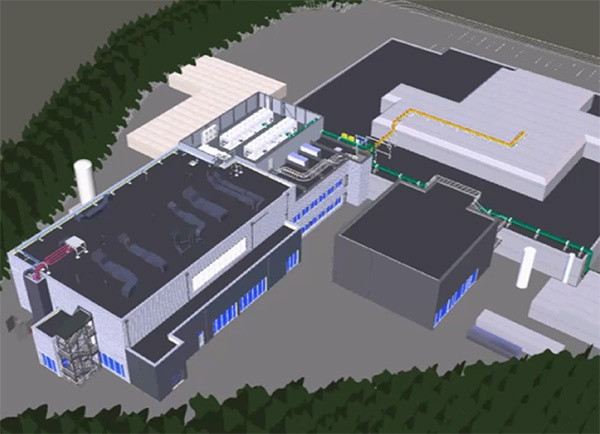
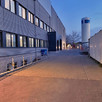
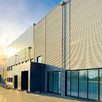
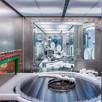
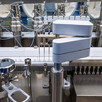
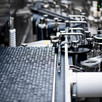
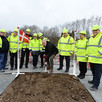
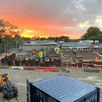
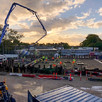
Project Experts
Similar Projects
-
Animal Vaccine Manufacturing Facility
Europe -
Vaccine Warehouse Storage Capacity Increase
Marietta, Pennsylvania, United States