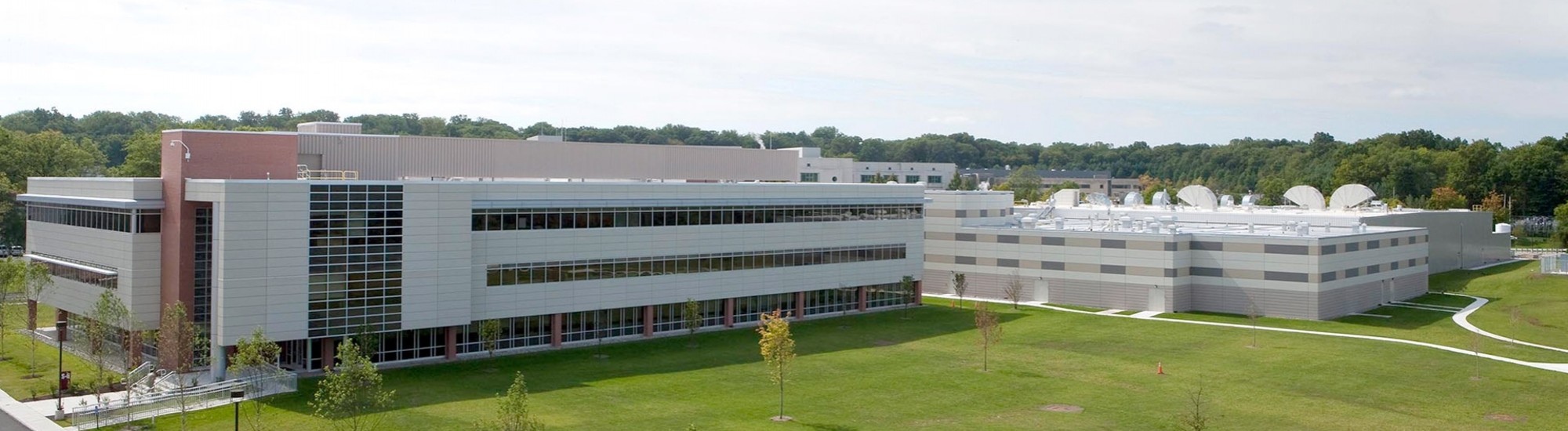
The flexible facility has the capacity to scale-up and deliver a variety of products simultaneously, including oral solid dosage, liquid, sterile and inhalation products for clinical trials. The facility was designed to increase capacity and technologies for core multi-product manufacturing and to support packaging and distribution of product for clinical studies. The expansion also provided the ability to grow and adjust to future growing product pipelines and to meet the strategic need of increased productivity and efficiency.
- Parallel production of multiple dosage forms
- Capability to support CGMP investigational drug product manufacture and process development operations up to 10% commercial
- Support primary / secondary packaging and labeling for clinical studies
- Local stability staging; calibration, testing, and maintenance; in-process testing and microbiology labs capabilities
- Flexibility and expansion for the introduction of new technology and adaptive reuse of existing technology with minimal disruption to site integrated containment technology aligned with development needs
- Potent compound manufacturing capability (1-10ug / m3)
- Optimized material / personnel flow facilitating direct movement from manufacturing to clinical supply packaging, reducing process steps and cycle time
- By employing a modular construction approach, we were able to meet aggressive deadlines, proceed with minimal site disruption and maximize utilization of existing infrastructure
- Hybrid modular/stick-built project consisted of 82 modules assembled in Sweden from frame to fit-out, including utility hook-ups, to completion in 27 weeks
- Involving the safety department during design resulted in a practical approach to remove potential hazards early
- Support accelerated proof of concept evaluation with minimal formulation development
- Harmonization of critical process equipment and technologies with R&D and commercial manufacturing
- Adjacency to key supply chain functional and technical units for rapid decision making and issue resolution
- Total project cost approximately 3% under budget
- GMP operations commenced 1 month ahead of baseline schedule
IPS Highlights
- Balanced cost/quality design to budget approach
- Designed/engineered with capacity for future fit-out and modular expansion
- Incorporates extensive energy, sustainability and “green” initiatives
- Center support piers were pre-cast allowing for a smaller 300-ton crane to be set within the modular building support foundation where it installed the building modules in a “C” pattern. Once the first portion of the module installation was completed, the crane was moved out of the modular building footprint, the pre-cast pier was moved into place and bolted down, and the installation of the building modules continued in an uninterrupted fashion.
- Modular building process/manufacturing foundations were constructed to a +2mm tolerance in preparation for receipt of the modules. A portion of the foundation piers were also designed to be removable in order to allow a more efficient and lower cost rigging approach.
- BOD to construction completion in less than 30 months
Region: AmericasCountry: United StatesOffice: Somerset, NJ
Services: Architecture, Process, Construction Management, Engineering, Strategic & Facility Master PlanningIndustries: Oral Solid Dosage, PharmaceuticalFacility Type: Manufacturing
Size: 237,000sfAwards: 2011 ISPE Facility of the Year Award for Facility Integration
Project Details
Region: AmericasCountry: United StatesOffice: Somerset, NJ
Services: Architecture, Process, Construction Management, Engineering, Strategic & Facility Master PlanningIndustries: Oral Solid Dosage, PharmaceuticalFacility Type: Manufacturing
Size: 237,000sfAwards: 2011 ISPE Facility of the Year Award for Facility Integration