The Lean Way to look at Modular Construction.
One painkiller doesn’t work for everyone—and a standardized approach to modular construction won’t work for every situation, either. A physician considers many factors, weighing risks and advantages, before prescribing an analgesic to obtain the desired outcome. Similarly, it makes sense to take a smart approach to building a pharmaceutical plant. A custom modular approach can maximize the benefits of modular construction for expansions and upgrades, as well as new construction, without sacrificing flexibility.
A different way to think about modular
In the world of pharmaceutical facilities, the term “modular” has come to imply a complete facility, organized in shipping container sized units, built at a remote location, transported to the owner’s address, and reassembled on site. The modules consist of structural frames fit-out with architectural elements. Mechanical, electrical and plumbing (MEP) systems and process equipment are already integrated. This approach offers many benefits—but does not fit the bill for expansions and upgrades to existing plants. For smaller projects, plant owners can take advantage of customized modular product delivery to reduce overall project schedules, increase quality with minimal disruption to site operations and potentially realize cost benefits.
Options include prefabricated process and utility equipment, such as skid-mounted clean-in-place or reheat equipment, pre-piped and pre-wired air-handling units (AHUs), modular penthouses complete with air handlers, chillers, and MCCs. Large “super-skids” can be broken down for shipment and reassembled quickly in the field. Another application of custom modularization is to employ modular wall systems and modular pipe racks for HVAC piping and ductwork, plumbing, process piping, electrical and controls.
Modular advantages and considerations
Modular project delivery (MPD) offers several significant benefits, including enhanced quality control, reduced waste, reduced impact on current operations and simplified site logistics. Transferring labor hours away from the owner’s site can reduce both cost and risk. For example, a pharmaceutical manufacturer needed a bump-up for an expanded fluid bed drying process. Building the addition on the ground and lifting it into place limited the shut-down time and minimized the number of personnel needed on the roof. The ability to build multiple modular elements in parallel, with no weather impacts, can reduce schedule duration up to 50 percent, and the ability to leverage factory acceptance testing often translates into shorter start-up and commissioning duration.
Modular project delivery also poses some challenges that make choice of a partner with experience in both MPD and technical construction critical to success. Full-plant delivery via shipping containers requires locking in the floor plan early in the project and can increase engineering costs. Modular projects require additional interface coordination—for example, oversight to ensure that all vendors meet local code requirements, construction materials used are consistent and compatible, controls are integrated, etc. It’s important to identify any potential maintenance or operational issues and to allow for future changes and renovations. Even logistics can be challenging, as transportation becomes a factor.
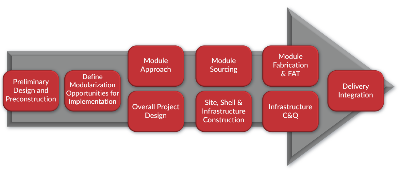
A “lean” approach to modular construction will reduce waste and cost, enhance quality and create a delivery system that meets owner requirements—for example, by limiting the length of a shutdown. The lean approach requires both insight and forethought. Rather than picking an off-the-shelf clean room module, lean means bringing contractors, subs and vendors on board during the design process and leveraging their knowledge to engineer a solution that meets the owner’s unique needs and goals.
The custom modular delivery process
The preliminaries are critical. In traditional project delivery, definition of physical details is deferred until late in the preliminary, or schematic, phase. In the custom modular delivery process, early design must address target systems and layout constraints, structural frame requirements, transportation and constructability constraints and flexibility for future capacity and system expansion. At this point, modularization opportunities can be identified for implementation. Three-dimensional modeling is ideal for defining intent and determining overall assembled weight. Moving even small portions of the construction off-site can reduce safety risk, minimize impact on operations and improve the shutdown schedule.
It is important to consider whether module vendors should receive a detailed layout versus performance specifications, and the manner in which interface coordination will take place in the shop and the field. In either case, documentation must be thorough. Any lift rigging necessary to put modular components in place must be planned as part of the construction coordination.
Just as the approach to modularization should be developed in parallel with overall project design, modules can be sourced while the site, shell and infrastructure construction takes place. Similarly, modules can be fabricated and factory acceptance testing performed as the infrastructure undergoes commissioning and qualification. These parallel activities can shave significant time from the schedule compared to the end-to-end timelines required for completely stick-built projects. A construction management partner that understands the entire plant life cycle can help maximize the benefits.
Process and facility modules ideal for custom modular
Process and facility modules can be designed and built offsite. When it makes sense, factory acceptance testing and pre-qualification can also be performed prior to shipping them—intact or disassembled. Once on site, the integrated construction and compliance team verifies receipt, reassembles the modules and performs final testing and qualification. One option that may make sense for many projects is modularization of utility generation and distribution systems. Designed to meet the required performance specifications, they can be prefabricated on special structural support systems, shipped just-in-time and assembled. The skidded modules generally require a smaller footprint than conventional distribution systems.
Today’s modular wall systems, which evolved from prefabricated PVC-sheathed aluminum frame wall and ceiling panels, offer a high degree of flexibility. Options include “walkable” ceiling systems and prefabricated return-air walls. Modular wall systems can incorporate integrated electrical lighting and receptacles, HVAC ductwork, HEPA filters and controls.
Modular makes sense
In summary, modular project delivery that does not take a cookie-cutter approach to every project offers a number of significant advantages for plant renovations and expansions. From a schedule perspective, performing activities in parallel can reduce overall project duration and make a very favorable impact on the critical “time from decision to delivery.” MPD reduces disruption to the site as well as lay down and waste area. Fabrication in the shop rather than the field results in higher quality work and, ultimately, better quality of the final facility. By reducing labor hours at the site, MPD improves project safety. Modular project delivery may also reduce costs by transferring labor to lower cost centers, taking advantage of higher productivity in the shop versus the field, and generally reducing site requirements. Throughout it all, a team experienced in technical construction can save a lot of headaches and help make sure that the owner sees benefits related to schedule, quality, safety and cost.