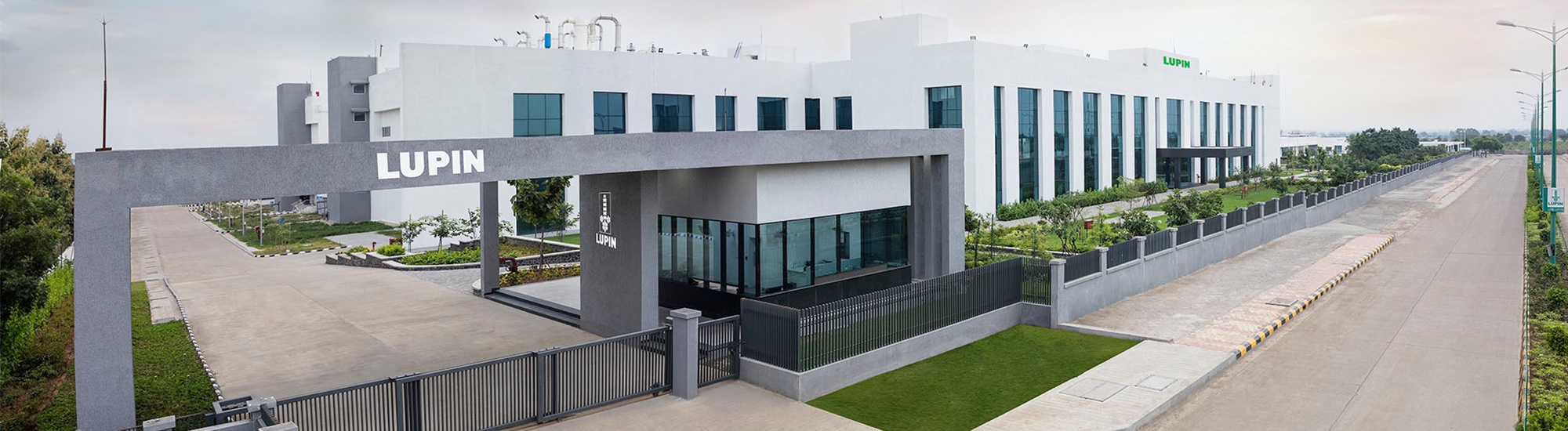
This ENR award-winning project demonstrates how integrating the industry’s best people with state-of-the-art technology, sustainable design, and global expertise produces a successfully implemented project that is both unique and ground-breaking in the Indian context.
The OSD manufacturing facility bottle line and bister line is designed for granules, tablets, encapsulation, and coating. The facility is equipped with fully ASRS for handling work in process and change parts, such as dies and punches with RFID code identification to eliminate human errors and mix-ups to ensure the highest degree of accuracy and productivity. To handle the vast quantities of bins and containers, a segregated and centralized automatic bin washing system was installed on the upper floor. This system circumvents the clustering of bins in the process area and keeps the corridors free.
The aseptic injectable manufacturing facility is designed to produce high potent compounds with multiple deliveries methods through different devices including liquid vials, lyophilized vials, cartridges, and pre-filled syringes. The fully automatic filling lines are integrated with a fully contained isolator system, and automated in-process check weighing and other advanced features to ensure accurate dosing and minimal rejects. The vial filling line’s integration with automated lyo loading and unloading ensures simple and repeatable transitions and the elimination of operator involvement using an isolator.
Both of the manufacturing facilities offer advanced technology for maximum flexibility and efficiency, and the extent of automation in the project, from auxiliary systems like HVAC controls to the production lines, indicates a new level of maturity in the Indian pharmaceutical landscape. This evolution is also evident in the importance placed on digital quality systems as well as systems for ensuring the reliability of the machinery.
The conceptual design study and detailed engineering design ensures compliance with the latest global regulatory requirements. Lupin adopted the latest project management and execution tools in the areas of project life cycle control, quality, team organization, and modular building systems to fulfill the objectives of meeting user requirements within budget and on schedule.
The strategic investment in the facility’s innovative process operational excellence approach maintains the consistent growth that Lupin witnessed across key markets, but it also ensures that all manufacturing capabilities are attuned for the future.
The facility fully incorporates all good engineering practices and the latest environmentally sustainable design features. The chosen equipment and its customized design were based on principles of optimizing efficiencies in power management, air-conditioning systems, compressed air installation, and lighting.
The Master Plot Plan is designed with a centrally located energy block with the production facilities placed within a convenient distance to achieve an integration of power, steam, compressed air, chilled and cooling water and primary treatment water generation and distribution. State-of-the-art systems with advanced automation were integrated efficiently to optimize the layout within the constraints of the available plot area. This led to better operational efficiency, centralized control, reductions in cost and materials, ease of operation, and aesthetic design.
A zero liquid discharge system is implemented to recycle and reuse the water. The rainwater is harvested and high-efficiency electrical equipment is used to save on power consumption. The engineering of the main plant and the building design are done in accordance with The Green Building Guidelines for maximum use of natural light in administration and QA/QC areas.
This fast-track project completed the design and execution in the minimum time of 42 months with 7.2 million safe man-hours.
The key to the success of this award-winning project was project leadership, coordination, and more importantly, alignment across all global parties. The team benefitted from a details project execution approach and various synergies that supported a mutual working relationship.
Region: IndiaCountry: IndiaOffice: Ahmedabad, Hyderabad, New Delhi, Mumbai
Services: Architecture, Engineering, Process, Commissioning, Qualification & Validation, Validation and Data Integrity ServicesIndustries: Pharmaceutical, Aseptic, Oral Solid DosageFacility Type: Manufacturing
Award: ENR Global Best Projects Award of Merit: Manufacturing
Project Details
Region: IndiaCountry: IndiaOffice: Ahmedabad, Hyderabad, New Delhi, Mumbai
Services: Architecture, Engineering, Process, Commissioning, Qualification & Validation, Validation and Data Integrity ServicesIndustries: Pharmaceutical, Aseptic, Oral Solid DosageFacility Type: Manufacturing
Award: ENR Global Best Projects Award of Merit: Manufacturing