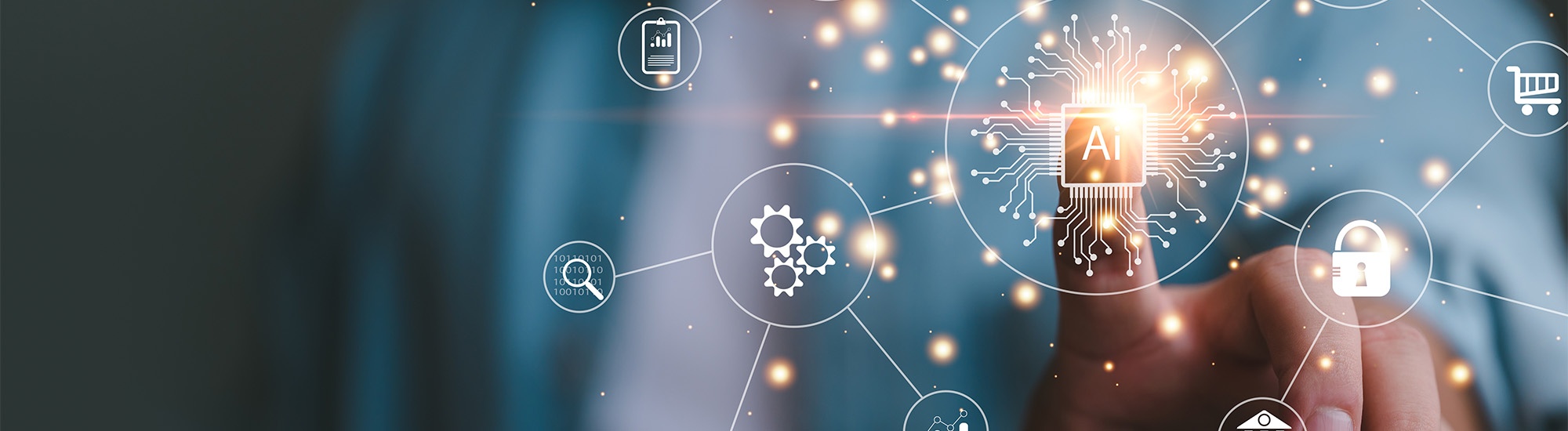
By Kevin Schreier and Ryan Campbell
The world around us is rapidly changing. From modern medicine breakthroughs to a worldwide health crisis response, life sciences manufacturers must turn their focus to speed and reliability. One way they are doing this is by employing advanced single-use systems (SUSs) in connected facilities. It is well known that single-use equipment can help manufacturers increase efficiency and profitability by simplifying production and reducing the need for clean-in-place operations. But when many think of single-use technologies (SUTs), they often think of low automation; when in truth, the next generation of SUTs is highly advanced and offers a wide range of flexibility that manufacturers need. These advances in SUSs help manufacturers add equipment that allows them to complete faster changeovers, provide flexibility in recipe management, and improve uptime. Technical advances are helping manufacturers get their pharmaceutical products to market faster while providing opportunities for increased automation. When the project goals are to maximize flexibility and data capture, while laying the foundation for digital transformation, early automation design collaboration is key to successfully starting up or adding intelligent technologies to a single-use facility.
Stage gates can create barriers to advances
For decades, the industry norm has been to take a linear approach to facility design and planning. An end-user would come to an engineering company, express their requirements for the facility, and much of the design and planning would be done with limited input from automation suppliers. This could lead to equipment not using automation, leveraging obsolete technologies or designs, and a lack of standards between equipment vendors. When it is discovered that an area could benefit from a modern automation solution (during detailed design, commissioning, or while in operation), significant rework may be needed. In addition, it is likely that the technology or infrastructure needed is not in place for this automation solution to be implemented, which can lead to even more work for the engineering and automation companies and additional costs for the end user. This rework and potential downtime for the machinery required while changes are made can also compromise data and operational integrity. Thus, when a gap in technology or automation efficiency is noticed, it requires immediate attention.
Bringing back the engineering company, original equipment manufacturers, software vendors, and end-user stakeholders to consult on the project is not only greatly inefficient but costly. What if the project took a different approach? The selected engineering and automation companies should collaborate from the planning and design stages of a project all the way through to the commissioning and qualification phases. This approach results in a more efficient, reliable, and modern design that is developed far faster than the traditional method.
The right people in the room
Some of the most successful companies in starting up or maintaining single-use facilities often share a common first step in getting the right people in the room early. At the beginning of a project, it is crucial that a representative from the end-user define the vision for the facility in its entirety. From engineering to manufacturing startups, this vision will help outline expectations, requirements, and a strategy for future development. The vision may involve the management of inventory in bag bins, active control of automated pinch valves, or preventative maintenance analytics, but it always requires multiple team members with different skills to realize this vision. The right representatives from an engineering, procurement, and construction (EPC) company and automation supplier also need to be involved early to allow for better knowledge sharing between the parties to positively influence the facility’s strategy and build the best solution for the end-user.
Early discussions are used by an engineering team to translate the end-users vision into a design basis that describes the functionality, device selection, map of the operational footprint, and how the process is being controlled. This effort usually requires a system integrator to be engaged who must work in parallel with the engineer to define control methodologies, document system requirements, code, define testing plans, support installation efforts, interact with software vendors, and so on. When these steps are not performed in parallel, delays or rework are common results. In addition, multiple vendors are commonly involved with different unit operations in biotech facilities, which means navigating competing priorities. The sooner the collaboration can begin, the better chance that standardization is realized across the project. Standardization is especially vital to better support employees who work with and maintain the equipment and technology day in and day out. Standardization is also important for facility-wide system integration between the equipment and higher-level manufacturing systems. Without it, data can be rendered unusable if it is incompatible with other information being collected or if it cannot be synchronized to offer visibility and insights into full operations. Stronger and earlier collaboration leads to the adoption of standards and, in turn, more useful data.
Keeping data integrity and extensibility in mind
Even if the right people are in the room to begin the single-use facility project, tight deadlines and multiple stakeholders can make it hard to manage priorities and make sure the facility design will meet expectations and pass the qualification process. As planning starts, there are two important considerations to keep in mind: data integrity and extensibility.
Perhaps one of the most important facets of data integrity when collaborating with multiple vendors, complex equipment, and critical data is cybersecurity. Typically, the more data that is generated, the more security is needed. In the early stages of planning, vendors may come in offering a new way to monitor reactors, but they might not consider that the camera they are suggesting would generate massive amounts of data that need to be stored efficiently and securely. Much too often, technology and automation solutions are planned or even get implemented that do not meet strict cybersecurity standards that life science manufacturers must maintain and become a liability that must be corrected. Workstreams must be kicked off to determine methods for secure storage of the data, and a retention policy must be developed. Keeping cybersecurity and data integrity a priority during early design collaboration will help achieve a more secure outcome for the critical data being generated and stored.
The other important consideration for an early automation design conversation is extensibility. If planning for any advancement in the future, how the facility is set up today could greatly impact the outcome. An attempt to automate or digitize a process later without the infrastructure to do so will be costly or could even become a lost cause. Being cognizant of the technical requirements for future automation or digitization plans helps to prevent this from happening. That is why engineering and automation staff working together as a team early in the project can enable the facility to extend and grow as technology permits collaboration as a team can also help confirm the right developments are being made to support the digital transformation journey and increase operational value. Answers to the following questions can help guide decision-making so that the right steps are being taken at the right time for a business:
- What benefits will be received (i.e., useable data, process improvements, etc.)?
- What level of automation can help improve quality or reduce safety concerns?
- Does it save money?
Without this input, it is possible to add technology where it is not needed or when it does not provide significant cost or efficiency savings. The earlier these conversations happen, the better the chance exists of receiving buy-ins from other key decision-makers and making the right decision sooner. Early buy-ins usually result in savings for the design, as technology and equipment can be carefully planned for, the proper resources allocated, and major infrastructure changes in the future avoided. Considering the data integrity and extensibility of the platform early in the lifecycle of the project can help maximize production at the facility and ensure there are no surprises or roadblocks when it comes to advancements in the future.
The collaboration should not stop
After the successful commissioning and startup of a facility, when the right people are involved early and all design and automation requirements are taken into consideration, maintaining strong relationships can offer even greater benefits. To ensure the facility is evolving to meet industry demands, a collaboration between EPCs, automation vendors, and original equipment manufacturers during the project should not stop after startup. Keeping the communication lines open for the implementation of new ideas and sharing of solutions allows for more efficient technology adoption when the time is right to implement a new feature or install a new component.
Staying aligned also means that standards can be regularly reviewed, and adjustments made to verify they are meeting current needs and are prepared to meet future business objectives. This will ensure that effort is not being spent to support something that is no longer relevant—further saving time and money. With the life sciences industry changing rapidly and increasing pressures for efficiency, manufacturers need to view the automation design process as a continuous collaboration for the entire lifecycle of their equipment and facility.
Why now?
As in many industries, the life sciences industry is entering a new era of digital transformation. Every new single-use facility is being built to be more advanced than the last, with the implementation of new equipment, components, and devices with higher levels of automation and the generation of more process data. These new smart facilities are creating a push for older facilities to quickly adopt the latest technologies and automation to increase their operational value.
As mentioned previously, single-use advancements are migrating away from their former manual state and can now be highly automated to optimize production and generate a wealth of insightful data. These new automation advancements need to be a key consideration at the start of the project and strategically planned for future implementation into the facility to more efficiently realize a facility’s potential. From design to qualification, a close automation design collaboration between EPCs and automation suppliers leads to better-informed and data-driven decision-making for the launch of intelligent single-use facilities.
Whether introducing automation into existing operations to further advance a digital transformation journey or embarking on a new single-use facility project, it is recommended to involve an integrated engineering and automation team who are ready to help identify strategies to achieve the business needs. Maximize the facility’s potential by involving your EPC and automation supplier early in your project discussions and by continuing this collaboration after the facility launch. By promoting collaboration during the planning and design phase of a single-use facility project, engineering and automation companies can achieve greater quality, operational, and financial efficiencies for their clients.
Published in BioPharm International.com