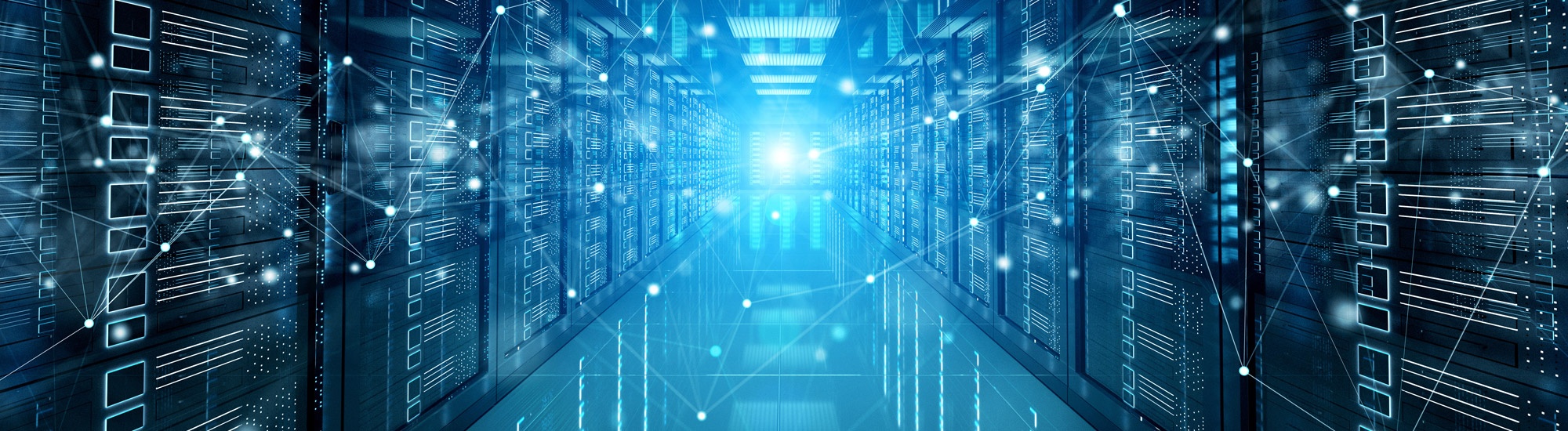
With over 30 years of experience and expertise in providing commissioning, qualification, and validation to highly-regulated industries, we understand the importance of rigorous planning, design reviews, inspections, and testing as part of a robust commissioning process. We have tailored our extensive history in commissioning processes to align with data centers, hyperscale data centers, high-tech manufacturing, and other complex facilities.
We provide independent commissioning services as defined by USGBC, LEED NC and EB requirements, ACG, BCxA, ASHRAE Guideline 0-2019 “The Commissioning Process” and other ASHRAE Guidelines, NEBB “Procedural Standards for Building Systems Commissioning, and SMACNA “HVAC Commissioning Manual.”
While many use a 5-level commissioning plan, we take ours a step further to plan for whole-building commissioning that goes beyond just a commissioning checklist.
Level 0: Planning and Design Review
The first level is often a collaborative effort between our commissioning team and MEP engineers. The commissioning team engages with the planning while the engineers provide a technical SME review of the facility/system design. Activities in this level/phase typically include:
- Development of an Owner’s Project Requirements (OPR)
- Define project requirements, scope, budget, schedule, Cx strategy, and develop Cx Plan
- Establish and gain team consensus on all commissioning forms, checklists, and reports
- Perform technical SME design reviews and commissioning based reviews
- Write commissioning forms and checklists
- Determine training requirements and conduct associated training of project stakeholders
- Establish software platforms to drive efficiency
- Define and implement document/information management and turnover strategies
Level 1: Pre-delivery Inspections and Factory Testing
Level 1 activities often play a huge role in maintaining critical schedules. Factory testing of major and critical equipment is inspected and tested at the vendor’s factory to confirm it conforms to specifications and delivers on the intended operating requirements. Initial factory inspections and testing can identify issues that can be resolved prior to release from the factory.
Level 1+: Modular Factory Testing
Level 1 + focuses on the quality, integration and testing of modular electrical, mechanical and technical rooms. Ensuring proper equipment installation & integration in the factory will reduce schedule impacts in the field. Performing pre-commissioning L3, L4 and L5 in the modular factory ensures the system is installed and configured correctly prior to being shipped to the site for final installation
Level 2: Pre-Installation Verification
Level 2 activities verify through physical inspection that the equipment and components delivered to the site match what was specified and approved by the engineer. This step occurs at the time of delivery and prior to installation to mitigate potential delays caused by the wrong equipment/components being delivered.
Level 3: Pre-Functional Testing
Level 3 is a milestone where the commissioning team’s on-site presence significantly ramps up. The pre-functional inspections are focused on checking that the equipment/system installations completed by the trade contractors, GC, and vendors have been properly installed per the project drawings, specifications, design details, applicable codes, and manufacturers’ stated installation instructions. Then verify that the systems are properly started up by the appropriate manufacturer’s representative.
After the equipment and systems have been verified to be properly installed, the energizing and start-up can proceed.
The pre-functional activities generally include, but not necessarily limited to, the following:
- General equipment and system installation checks (wiring, ductwork, piping, etc.)
- Pre-functional verifications for power, rotation, pressure hold testing, leak inspections, cleaning/flushing, etc.
- Manufacture specific start-up checks
- Verification of required operating training
- Ensuring safety measures and safe operating procedures are in-place to proceed to function and site acceptance testing
Level 4: Functional Testing
Level 4 is a milestone “where the rubber meets the road” in the commissioning process. The execution of the functional testing requires a high level of coordination with the many different contractors and vendors that need to participate and demonstrate the functionality of the respective systems. A single point of failure, especially as related to automation, can critically impact the overall schedule. The following building systems, all of which IPS has significant design, installation, and commissioning experience, are all functionally tested in this phase:
- HVAC systems
- Building automation and monitoring systems
- Electrical distribution, emergency power, UPS, and grounding systems
- Boilers, steam and condensate, and heating hot water systems
- Chillers and chilled water systems; supplemental cooling systems
- Piping systems
- Fire alarms and suppression systems
- Critical architectural details
- Lighting systems
Level 5: Integrated System Testing
Level 5 is testing of the entire building and a compilation of all equipment and systems operating in their intended steady state. The focus will be on proving that all systems work together and meet the expected design and user-defined requirements. At this juncture, testing is critical for the owner to have the required assurance to sign-off and take ownership of the building for beneficial use.
The testing primarily focuses on the electrical and mechanical systems and typically includes, but is not limited to, the following:
- Electrical integrated testing
- Electrical load bank testing
- Heat load testing
- Building automation and monitoring of in-operation conditions
Level 6: Close-out, Handover, and Owner Acceptance
The culmination of the new facility commissioning effort is the close-out, handover, and owner acceptance phase. During this phase the following activities are completed:
- Close-out of any final punchlist items or identified deficiencies
- Completion of any open Cx inspections or tests.
- Initiation of warranties
- Final evaluation of monitoring data of in-operation performance
- Transfer of document management and project files
- Owner acceptance and turnover
Level 7: Operational Qualification and Readiness
To ensure the successful operations of facility was the construction and commissioning process is completed it is important to ensure the operations team has the proper resources they need to effectively operate the facility.
- Development of emergency operating procedures
- Development of troubleshooting and response guides
- Operation and maintenance program development
- Training program development
- Method operating procedures
- Alarm and trend management