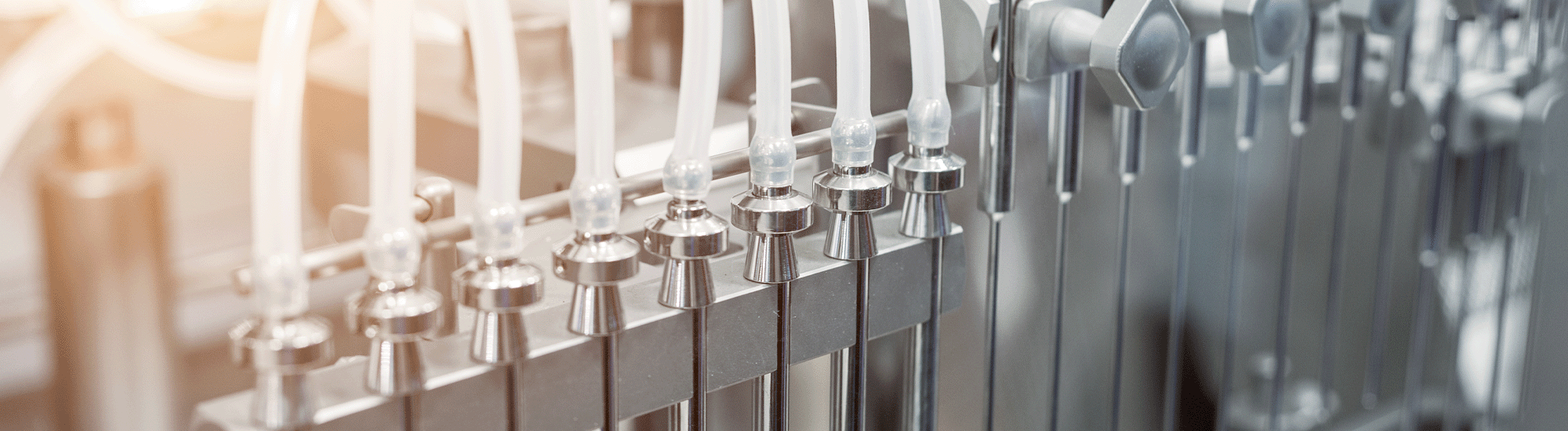
How rethinking project delivery and setting aside controls leads to meeting extraordinary production goals
by Hermann Schilling and Helmut Steudel, IPS-Integrated Project Services (Germany) GmbH
In June of 2021, IPS Germany was engaged to support a large Swedish CDMO in developing a COVID-19 vaccine production facility to serve the French market. A project that ordinarily would have taken 30 months to deliver is being delivered in 18 months. The term ‘fast track’ was never used on the project because the focus was entirely on what extraordinary steps could be and needed to be undertaken by the participants to reduce time and to eliminate constraints that typically cost time.
The brownfield site in western France comprises an aseptic filling line including formulation, inspection, leak testing, secondary packaging, and utilities and facilities infrastructure.
To ensure timelines were met, IPS established a collaborative approach. That required not just effort to integrate the various participants but also to be hyper-aware of cultural differences and communication behaviours that would impact the alignment and commitment. This approach lends itself to a time & material contract for the engineering, validation, and management services in order to ensure a very high responsiveness and adaptability. It also required strong leadership to maintain budget control and agreed contingency levels to react to unforeseen changes.
Good practices were undertaken to achieve the velocity required to meet the schedule targets, along with special steps to bridge the culture gaps between the various participating entities.
- Establish URSs for all process equipment and utilities within two weeks of kick-off. This was an extraordinary effort on behalf of the process team but set the stage for all other activities.
- Parallel to the development of the URSs, letters of intent were issued to long lead equipment providers to ensure production slots in very busy factories.
- Chinese process equipment suppliers were engaged for the first time in Europe because they were able to commit to a delivery time of 8 months.
- Standard equipment was used in all cases.
- URSs were reviewed and aligned between vendors and the owner in parallel with the equipment order to shorten the time.
- Virtual FATS were conducted to speed up the project and eliminate travel to the vendor locations.
- A leveraging strategy offers a schedule advantage by using the FAT/SAT test results in the IQ/OQ.
- Modular cleanrooms were manufactured in Spain and installed at the site.
- Detail design was done by the contractors in a ‘design-assist’ modality. The construction phase started earlier as the sub-contractors have been involved during the ‘design assist’ phase, potentially reducing the level of technical queries (TQ) as well as developing the design with a preferred buildability method.
- The BIM model was frequently federated with inputs from the various contractors to ensure clash clearance.
- Daily PMO alignment meetings were conducted to address continuous changes, maintain alignment among all stakeholders, and continually drive a minimal change and maximal adaptability philosophy.
- The qualification process was started in basic design phase.
- The owner’s project manager had over-riding authority and cover to make decisions and adjust to evolving needs in real-time with limited constraints.
One critical element pervaded the entire program from outset to completion: a commitment to achieve the schedule goals, even when that required adaption of corporate governance practices. Although cultural and communication differences often made for challenging moments, a shared vision and goal provided the motivation to move toward the ultimate outcomes.