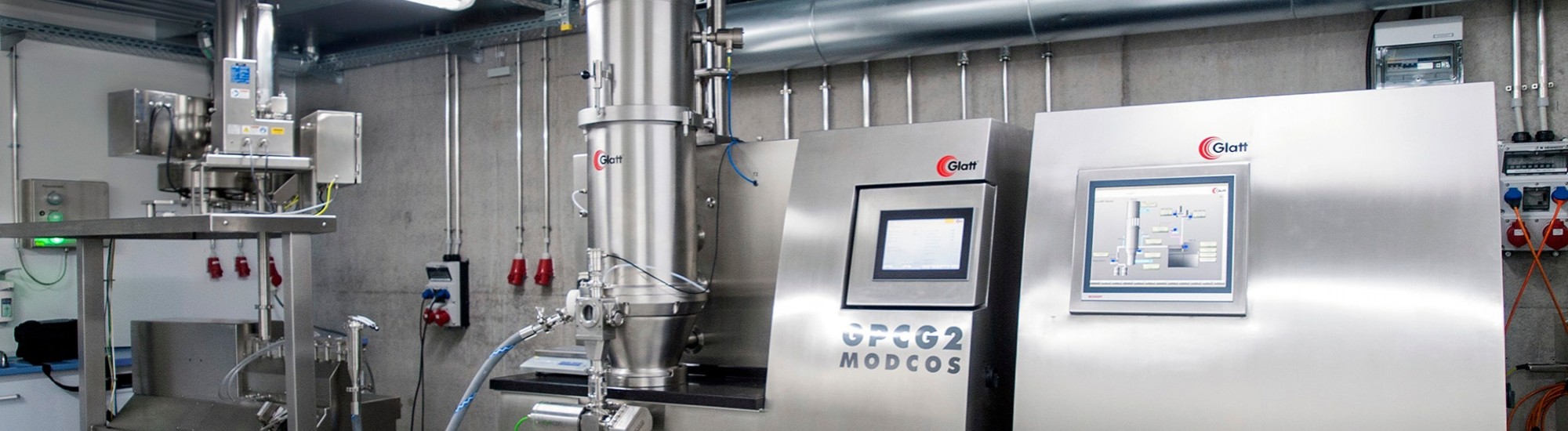
Continuous Manufacturing Principles – Linking Unit Operations and Eliminating Intermediate Bulk Storage
December 31, 1969 | 7:00pm and 7:00pm
- Overview
- Tour LeadersLeaders
- Vendors
- Location
- Vendors
- Location
As companies seek new ways to decrease capital expenditure and operational costs, as well as increase efficiency, continuous manufacturing (CM) has become a valuable practice within the pharmaceutical and biopharmaceutical industries. Both OSD and bioprocess unit operations have been part of the growing trend of continuous operations. CM provides the ability to increase equipment utilization and decrease hold-up times and volumes, making facilities leaner and more efficient. This Tour highlights the different continuous unit operations for pharmaceutical manufacturing and how they positively impact facility planning.
Share this Event
-
Theodore Cohen, MEM
Process Engineer
View Bio
Ted has almost a decade of experience in the biotechnology and pharmaceutical industries. He is deeply involved in process development and the commercialization of various manufacturing technologies. Ted has led extensive process modeling efforts and is practiced in equipment design, specification, and procurement. Throughout his career, he has gained a working knowledge of upstream and downstream unit operations and has designed critical utility installations including PW, WFI, clean steam, and pharma air. He has created deliverables for Conceptual Design, BOD, and Detailed Design phases and the generation of BFDs, PFDs, and P&IDs, as well as engineering calculations, design specifications, and equipment and instrumentation component lists and datasheets.
Ted has almost a decade of experience in the biotechnology and pharmaceutical industries. He is deeply involved in process development and the commercialization of various manufacturing technologies. Ted has led extensive process modeling efforts and is practiced in equipment design, specification, and procurement. Throughout his career, he has gained a working knowledge of upstream and downstream unit operations and has designed critical utility installations including PW, WFI, clean steam, and pharma air. He has created deliverables for Conceptual Design, BOD, and Detailed Design phases and the generation of BFDs, PFDs, and P&IDs, as well as engineering calculations, design specifications, and equipment and instrumentation component lists and datasheets.
View Bio
-
Lonna Gordon
Process Engineer
View Bio
Lonna has over 7 years of experience in GMP manufacturing with a focus on oral solid dosage process system design, from concept through construction. She has a strong background in contained powder handling, powder transfer, equipment design and selection, and capacity analysis. Her projects have ranged from multi-story gravity-fed wet-granulation trains to compliance remediation for generics manufacturing. Her biotechnology experience has encompassed aseptic formulation and filling, including both equipment and clean utilities design, giving her a well-rounded perspective on the industry.
Lonna has over 7 years of experience in GMP manufacturing with a focus on oral solid dosage process system design, from concept through construction. She has a strong background in contained powder handling, powder transfer, equipment design and selection, and capacity analysis. Her projects have ranged from multi-story gravity-fed wet-granulation trains to compliance remediation for generics manufacturing. Her biotechnology experience has encompassed aseptic formulation and filling, including both equipment and clean utilities design, giving her a well-rounded perspective on the industry.
View Bio
-
Michael Vileikis
Director, Process Technology
View Bio
Michael has more than two decades of experience in the pharmaceutical and biotechnology industries. He offers a broad range of technical knowledge and skill, specifically in the areas of process system design, containment and material handling strategies, equipment specification, and utility system design. Michael adds value to all phases of a project from concept/feasibility to detail design and through construction administration. Michael’s experience with OSD manufacturing, aseptic/sterile filling, and biotechnology facilities have allowed him to develop a depth of knowledge of the equipment, processes, operations, and material handling requirements associated with these facilities.
Michael has more than two decades of experience in the pharmaceutical and biotechnology industries. He offers a broad range of technical knowledge and skill, specifically in the areas of process system design, containment and material handling strategies, equipment specification, and utility system design. Michael adds value to all phases of a project from concept/feasibility to detail design and through construction administration. Michael’s experience with OSD manufacturing, aseptic/sterile filling, and biotechnology facilities have allowed him to develop a depth of knowledge of the equipment, processes, operations, and material handling requirements associated with these facilities.
View Bio
Jacob K. Javits Convention Center
7:00PM and 7:00PM
655 W 34th St | New York, NY 10001
The IPS Technologies Tours at Interphex will take place at the Javits Center. Please meet in the Glass Room at the Javits Center.