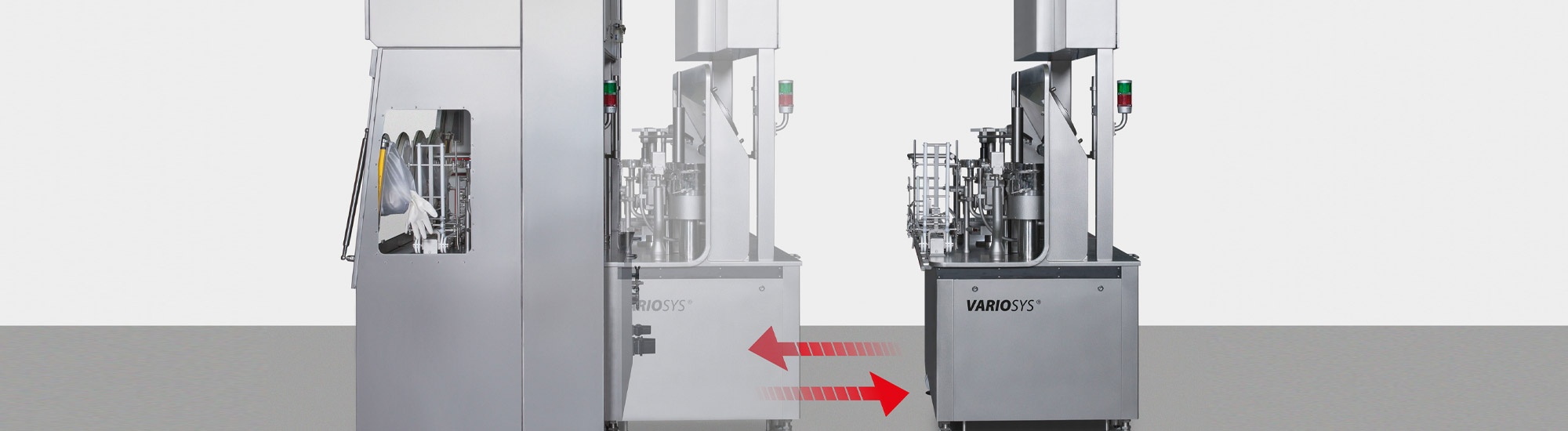
It will be possible to design a large proportion of full-scale, isolator-based aseptic filling lines with most required systems and utilities under the typical 10 feet (3 meters) clean room ceiling in the near future.
Will you join me in this vision? I am sure other stakeholders in aseptic fill-finish manufacturing share this desire.
Such an achievement will be highly valuable to the pharmaceutical industry. Current solutions and trends in process technology indicate it is feasible, and perhaps around the corner.
The industry has benefitted greatly from early pioneers of advanced aseptic technology: companies and individuals that pushed the envelope in the past. New filling lines provide greater flexibility, reliability, and higher yields through improved component handling, more accurate dosing, advanced automation, and minimization of waste.
Isolator systems provide a quality environment that separates people from aseptic processes and the systems perform automated bio-decontamination cycles, now under two hours. An isolated filling line with state-of-the-art functionality has become feasible for more and more companies, whether they are branded, CMO or generic injectable drug manufacturers.
More progress is needed.
There are still many pharma manufacturing sites, some say hundreds to thousands worldwide, that perform aseptic manufacturing in traditional Grade A clean rooms, relying on fully gowned operators to perform their trained aseptic technique with consistency. They have limited capital, or perhaps limited knowledge of today’s possibilities. World regulatory agencies are applying pressure for barrier technology to make this history.
Today, manufacturers with legacy facilities planning upgrades are often looking past Restricted Access Barriers (RABS) and choosing isolator technology once they understand how much isolator design robustness and affordability have improved.
Despite advances in isolator-based filling lines, the need to position significant air handling equipment above the machine adds cost and required space, making this option out of reach for some companies.
I see equipment suppliers already embarked on the vision for more compact full-scale lines. Significant strides in aseptic processing and filling technology are flashing before the pharma industry quite rapidly these days. Transformation of leading suppliers from pure equipment builders to solution providers has a lot to do with the significant progress.
Gone are the days when a supplier would react with an attitude of, “you want me to make your machine do what?” Instead, suppliers understand the quality and process requirements of the pharma industry. Not only are they eager to meet the challenges requested of them today but they also have stepped up to proactively advance process technology in collaboration with drug manufacturers.
One such collaboration spawned the development of small-scale, modular systems with a ‘plug and play’ approach. Bausch + Stroebel partnered with isolator supplier, SKAN, to develop VarioSys®. The initial concept used a sterility testing isolator platform designed to fit into lab spaces, i.e. below the ceiling, allowing companies to fill vials one day and syringes the next, all on one platform.
A new solution was born. Filler supplier, groninger, and Franz Ziel now offer a similar combined product, called FlexPro. Vanrx Pharmasystems designed its small-scale robotic and isolator-based filler from the ground up, neatly designed for easy installation.
Meanwhile, advances in isolator design for full-scale lines have resulted in more efficient and compact air handling. Bus-sized air handlers from the past have become compact modules. Some solutions already incorporate all air handling on top of the isolator footprint, albeit above the ceiling.
One can see a natural progression, making isolators for full-scale lines look more and more like those used for the smaller scale systems. There are technical challenges to make the full scale filler/isolator systems even more compact, but recent developments clearly show that solution providers are up to the task. Just as the modular systems have opened up isolator-based filling to many companies on a smaller scale, the proposed step change for more compact full-scale lines will also have a significantly positive impact on the industry.
The vision I put forth is not a ‘man on the moon’ moment. My colleagues and I have a few ideas of our own, and the star wheels are already in motion with current design trends. It is simply a matter of time and priority. Let’s do what our industry does best and collaborate to make it happen.
This originally appeared on Pharmaceutical Processing World.