Factory Acceptance Testing
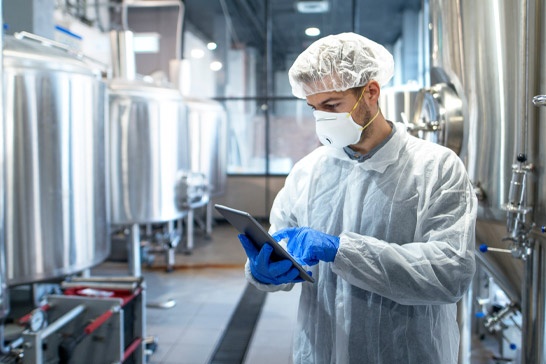
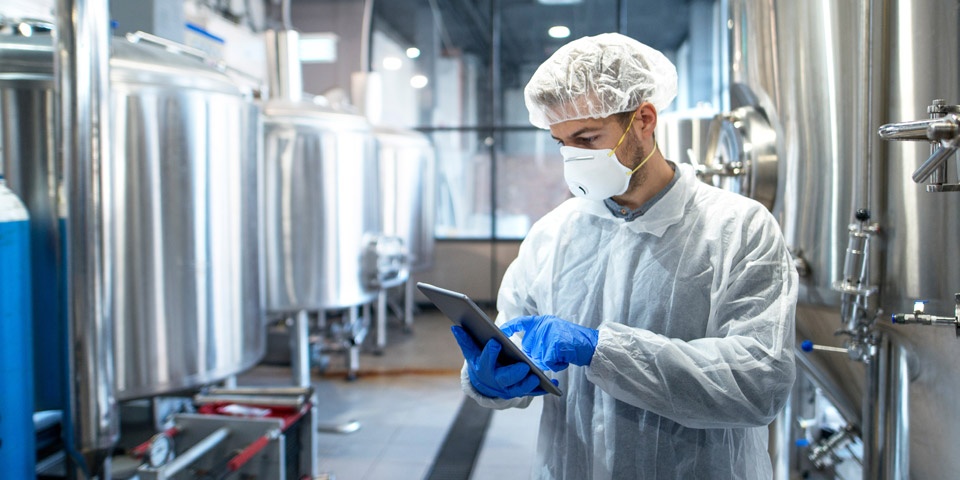
The Factory Acceptance Test (FAT) of new equipment is a critical component in optimizing operational readiness and reducing long-term costs. FAT allows for assessing whether the procured equipment aligns with set quality and safety requirements and addressing any punch list items prior to the equipment arrival for Site Acceptance Test (SAT). By leveraging the expertise of a specialized consulting firm such as IPS, our clients can not only ensure a thorough FAT process with Good Engineering Practices (GEP), but also maximize their investment’s value throughout the equipment’s life cycle. Utilizing our experience with ISPE Baseline® Guide for Commissioning and Qualification, and ASTM E2500 Standard Guide for Specification, Design and Verification of Pharmaceutical and Biopharmaceutical Manufacturing Systems and Equipment, we provide insights into FAT challenges. IPS can help prevent potential downtimes, costly post-installation modifications, and unforeseen operational inefficiencies for our clients. IPS can be an invaluable ally during the FAT process.
Pre-FAT Strategy & Planning
- Deep Dive into Documentation. Our experienced professionals rigorously review key documents like User Requirement Specification (URS), verification matrix, and functional specification (FS) to ensure each function of the equipment can be directly related back to our client’s design requirements.
- Customized FAT Protocols. IPS leverages extensive experience in crafting FAT protocols for specific equipment to identify testing gaps and resolve them by considering additional testing, i.e., SAT.
Aligning Testing & Documentation with Business Objectives
- Safety First. Beyond operational efficiency, IPS can verify that equipment meets safety standards, and does not pose hazards to individuals or the facility.
- ROI-Centric Testing. IPS uses integrated science and a risk-based approach to test and verify critical aspects of equipment which directly impact ROI and quality requirements.
- Strategic Future-Proofing. IPS emphasizes tests that verify the equipment’s current functionality while also evaluating adaptability to potential future changes.
Efficient Handling of Punch List Items
- Proactive Approach to Potential Challenges. IPS uses our experience to anticipate common challenges such as use of 3rd party components and test equipment issues and address them to ensure that FAT is executed efficiently.
- Punch List Management. IPS documents and provides timely support to resolve unexpected deviations or retests with accurate results without prolonging schedules. Documentation of steps taken to resolve punch list items ensures traceability and opportunities for continuous improvement.
Post-FAT Support
- SAT, IOQ, and PQ Support. IPS provides guidance during on-site installation and operational qualification stages.
- Customized Learning. IPS provides customized workshops tailored to specific equipment, ensuring our clients’ staff are equipped with the knowledge to safely operate, troubleshoot, and maintain equipment.